Insertion & Ejection Mechanism and Encasing for Small Cylinders into Central Console
I was tasked with designing the mechanism that would reliable acutate and move the cylinder throughout the four distinct moments of game play. Some design paradigms I considered included:
- Design For Assembly: By multiple persons, in a 3 week turnaround from Concept Refinement to Final Presentation
- Design For Manufacturing: Functions could still be reliably executed with a simple manufacturing in lab. Can also be quickly prototyped for functionality even if weight and material properties of Smaller Cylinder were still undecided.
- Design For Flexibilty: That would withstand are disaggregate design process ocurring by each team member working on different components.
Prototyping Mechanisms
First, I had to prototype a mechanism that could "do" all the four game design positions, all in the same encasing.
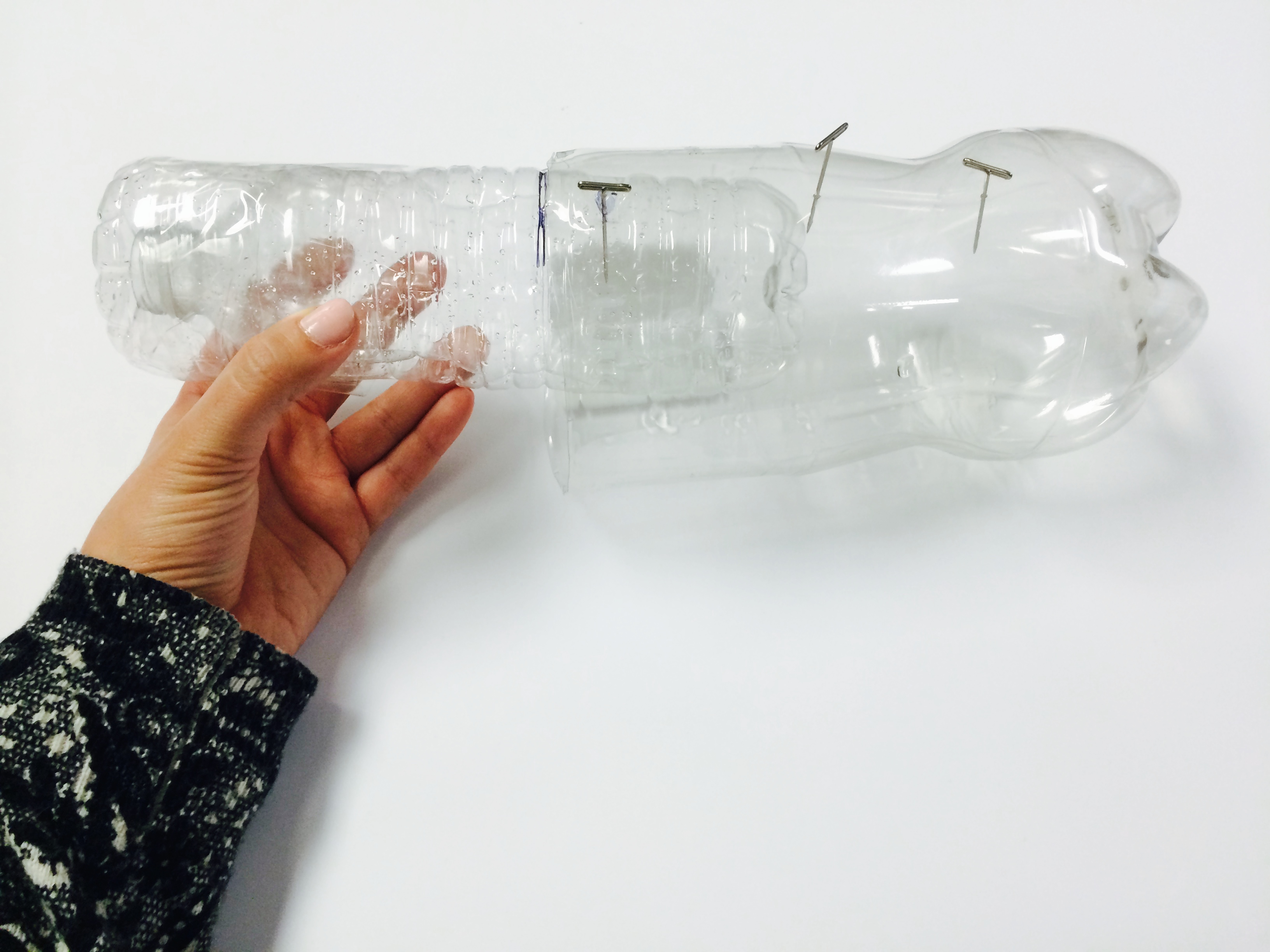
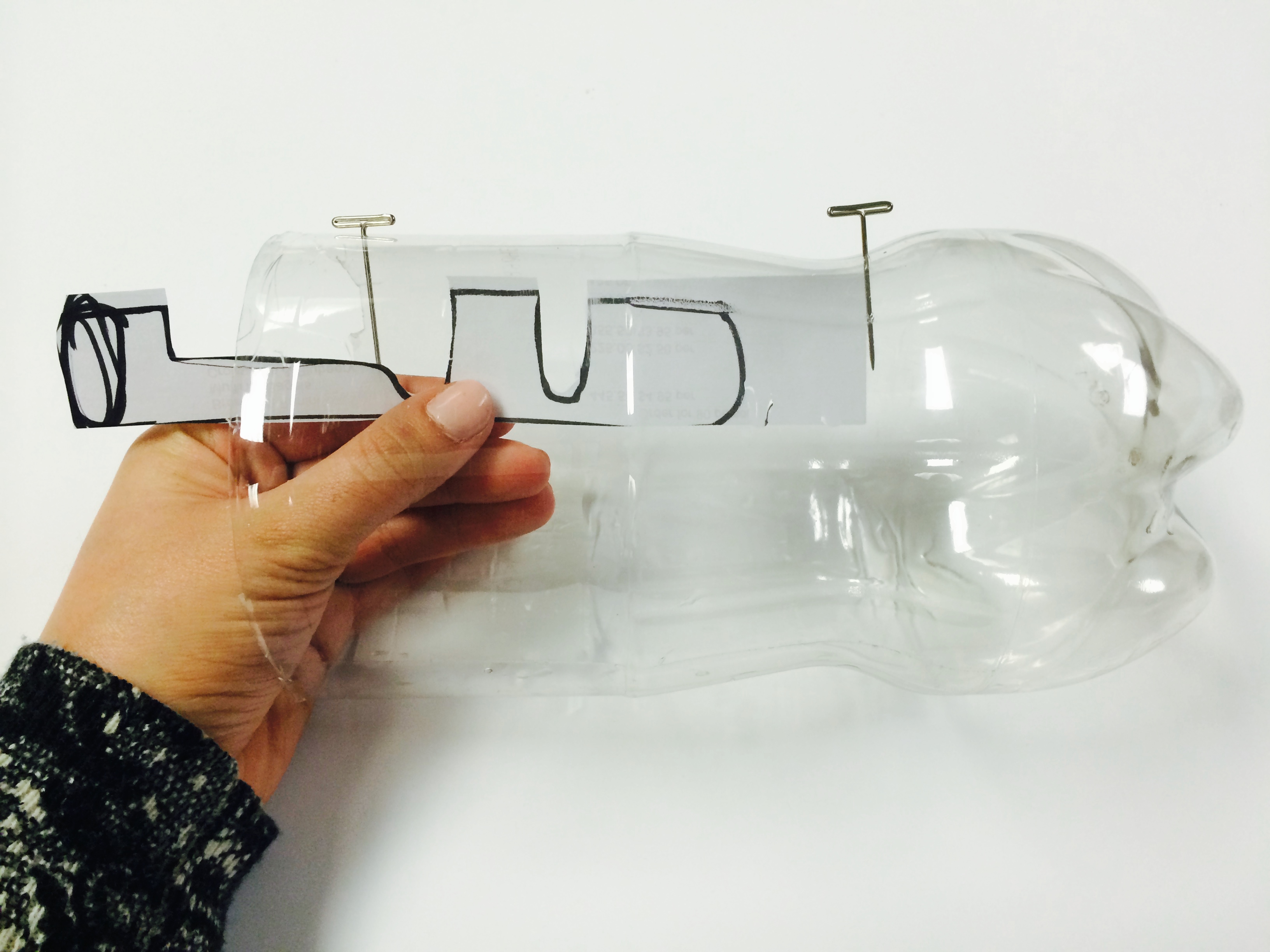
I made a quick mock-up of the cylinder to understand how it would move through the different gameplay positions, and realized that a basic mechanical stopper would be best for different levels.
I realized that by fixing the Small Cylinder to a counterweight that would stay on the inside of the console, we could fix a potential cantilever problem, and be able to dig notches into counterweight for the stopping mechanisms to go on behind the scenes. These would not be visible to the user and therefore wouldn't detract from the user experience.
The images below show the 4 different positions the cylinder would have to move through in order to suffice the user's gameplay experience. The aluminum pins represent the positions of the stopper block.
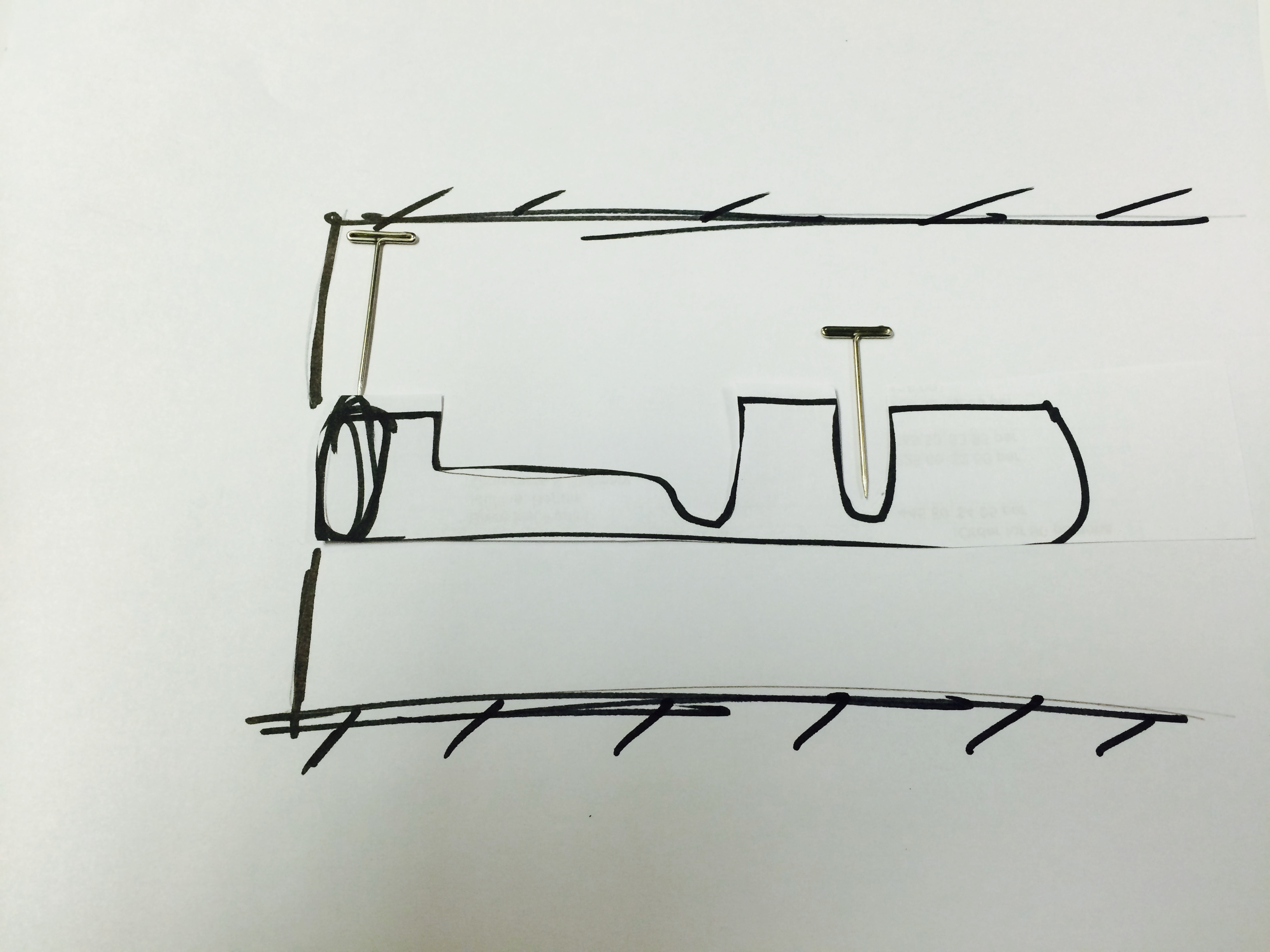
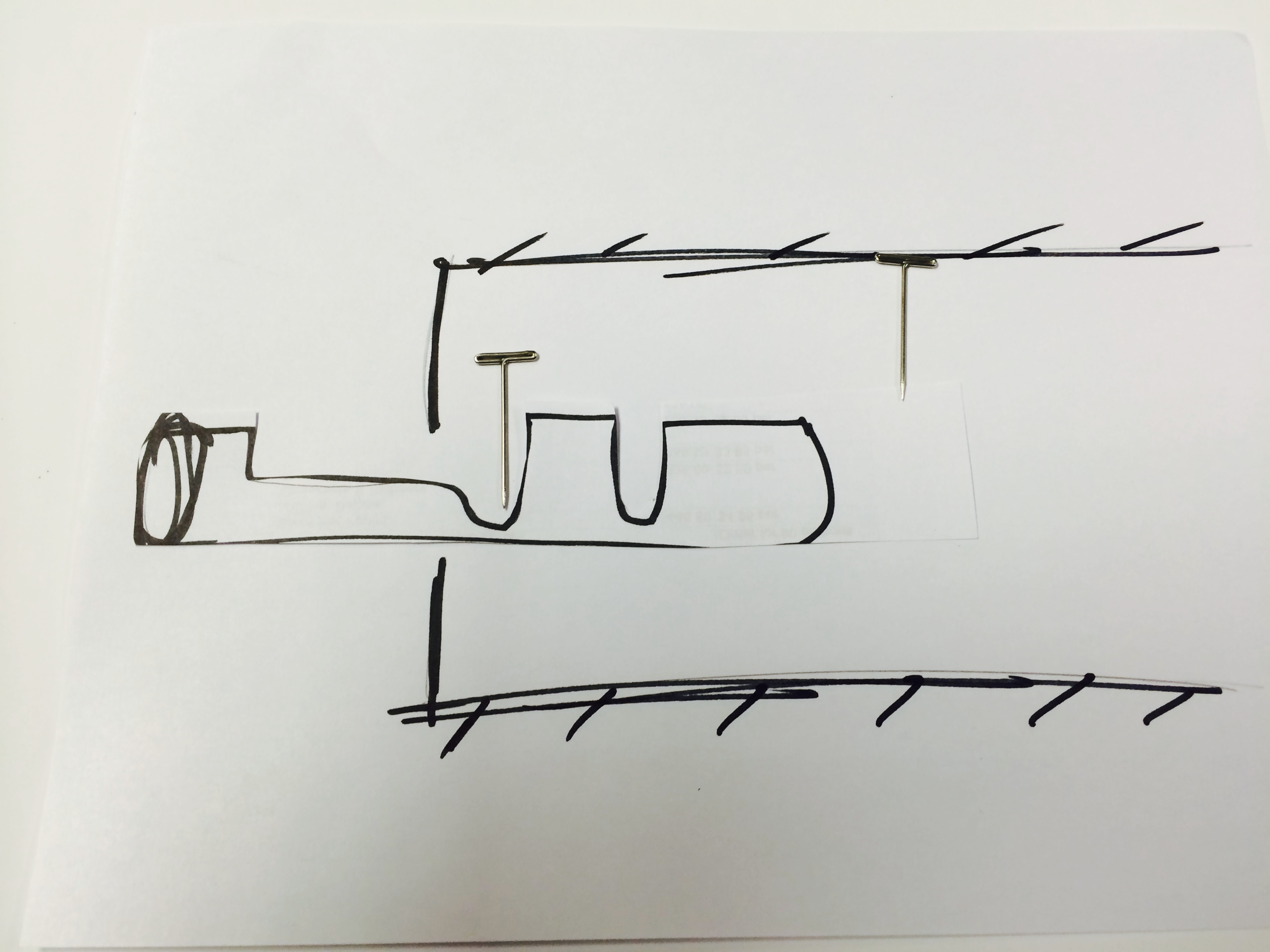
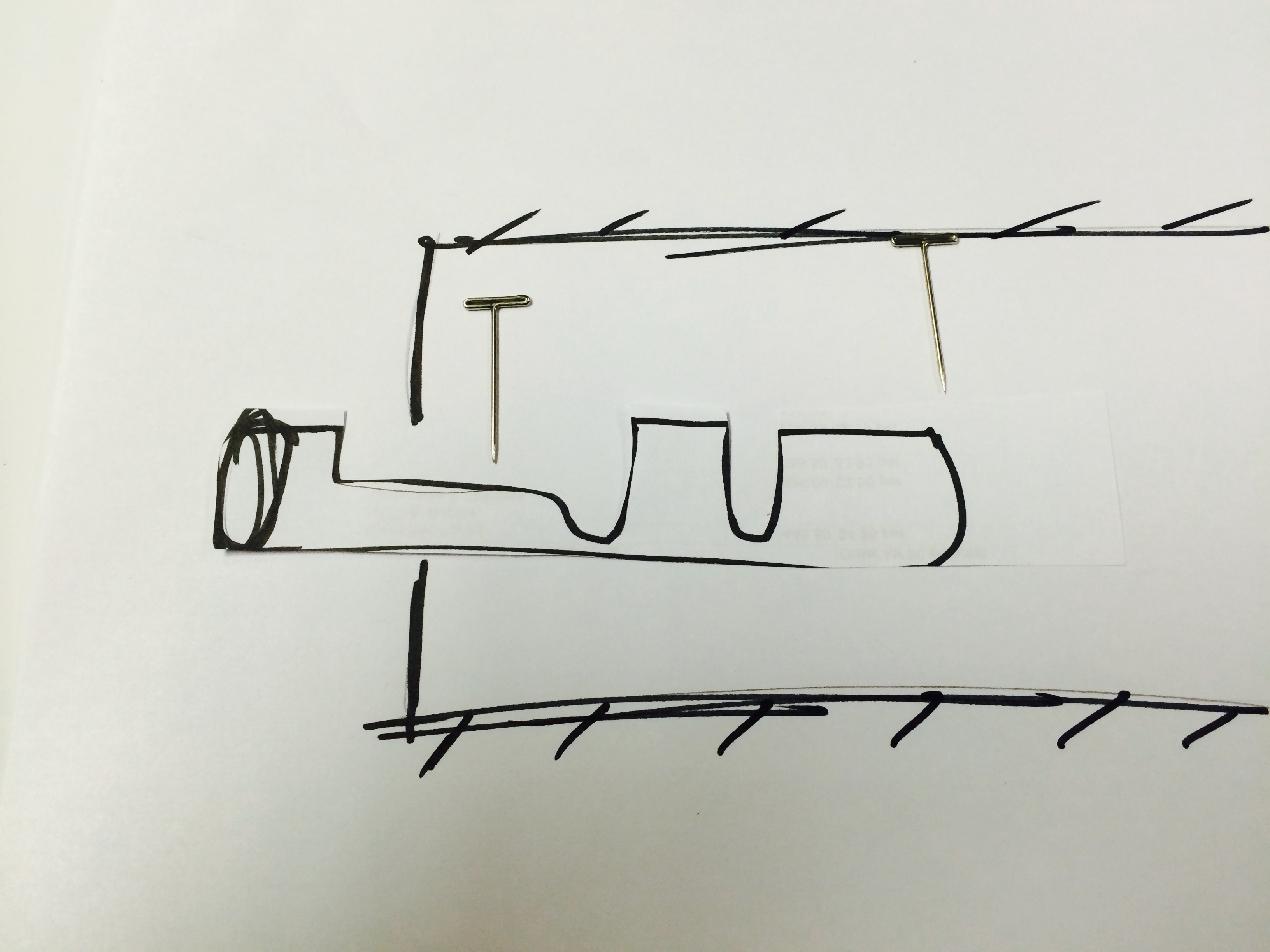
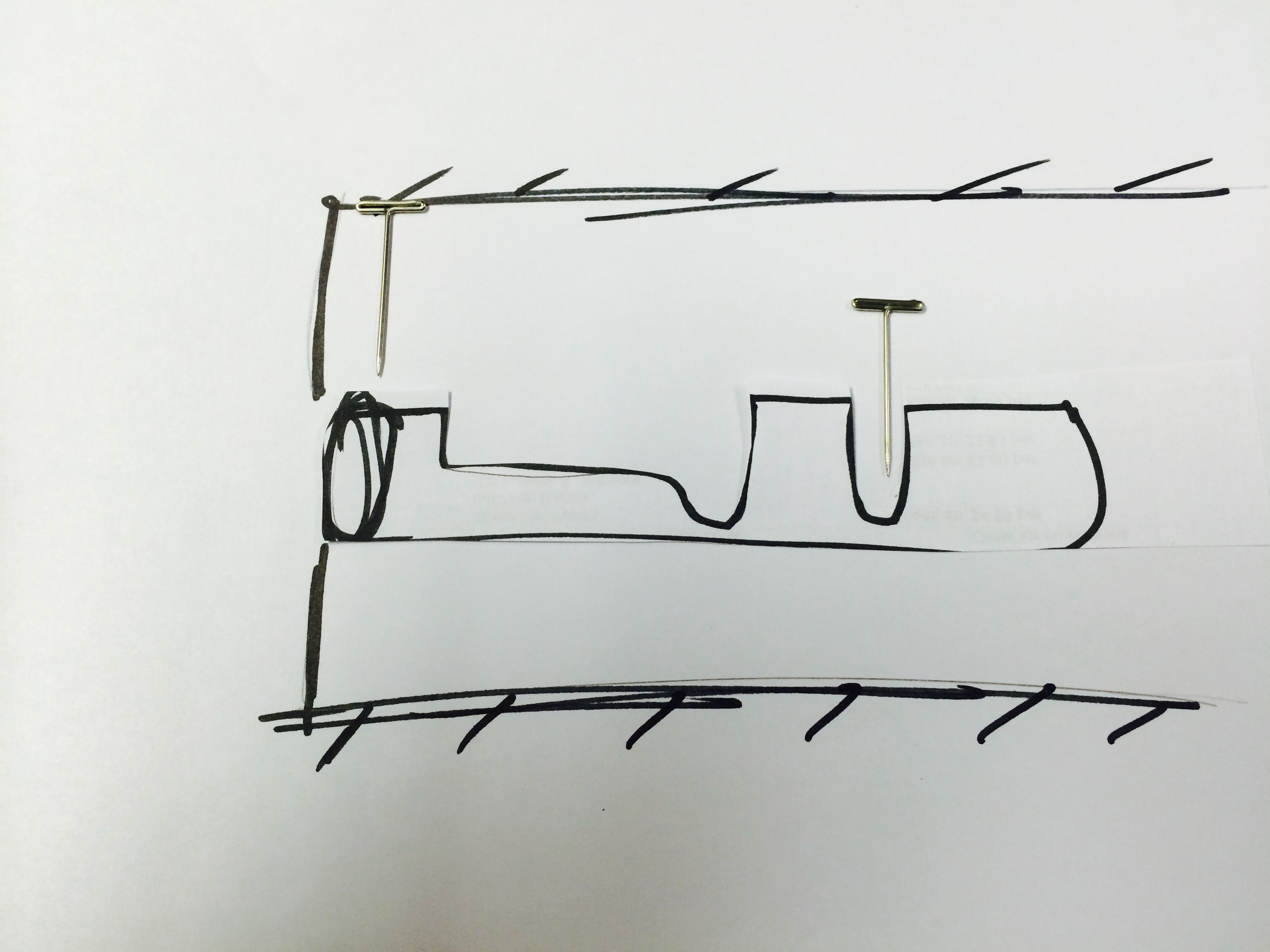
Cadding the Insertion & Ejection Mechanism and the Encasing
After manipulating some geometric properties and doing the multiple calculations of size constraint (informed by the overall dimensions of the Center Console decided by the team's U.I. focus) I CADded for a lower estimate of a 2' Small Cylinder in order to have enough space for the counterweight to fit inside the console.
I decided on a design with a rectangular counterweight containing 2 distinct notches on top for two different stoppers driven by a servo or stepper motor. The counterweight would move on precision rails (similar to fancy drawers railings) and have a spring on the back attaching it to the encasing to further prevent any clashing.
Some key features include:
- A counterweight fixed to the Small Cylinder: While the cylinder is free to rotate, it is attached to a non-rotating counterweight inside the console, completely hidden from the user.
- Square profile on a the counterweight: This allows for redundancy in ensuring the cylinder will not fall out of the console when ejected (in case there is electronic controls failure).
- 2 notches on the counterweight: Dimensions are driven by the half length of the Small Cylinder, and can be easily machined to accommodate any size stopper
- 2 stoppers going through the top wall of the encasing, activated by a servo or stepper motor connected with PWM (Pulse Width Modulation) signals on the controller
- 2 precision rails for the counterweight movement: This builds on existing technologies that are simplest to incorporate, test, and later modify according to different specifications (load resistances dependent on eventual changes to the final weight of the cylinder due to different materials chosen)
- A dampening spring: This is attached from the back of the counterweight to the back, inner wall of the encasing in order to account for over-excited users that may want to slam the Small Cylinder back inside the console.